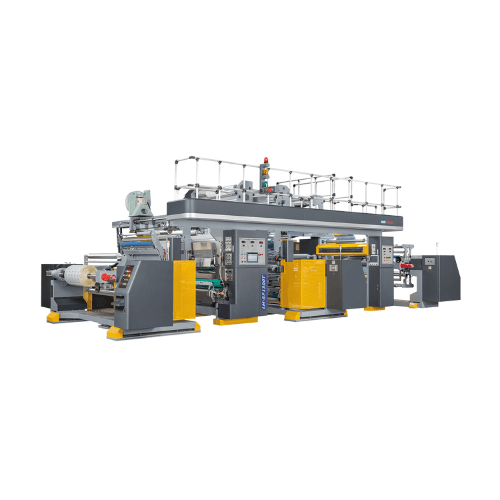
Turret Type Solventless Laminating Machine LM-SF1300T
Categories : Industrial Lamination
- SHAFTLESS-INSERT TYPE BUSHING - Turret Type Shaftless Unwind & Rewind - Coating Head Consists of 5 rollers with 3 independent motor drives for doctoring roller, dosing roller sleeved transfer roller and coating roller. - Sleeved Transfer Roller The sleeved transfer roller is more lighter and to be taken out quickly. - Non-stop & Auto Splicing Auto splicing for non-stop production Low waste during roller changes
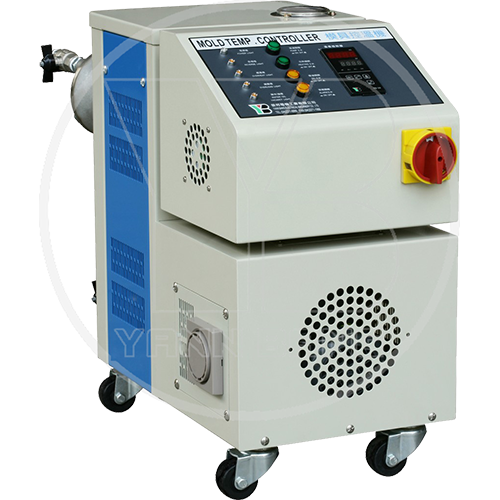
Compact Water-type Mold Temperature Controller
Categories : Control Equipment
Size decrease 50%!You can place the unit under the molding machine or small place by your need easily. All functions are the same but become smaller and lighter! You can place the unit on floor or on a working platform for better working environment. Patented “Heat-insulated” design (China Pat. 01345946.5; Taiwan Pat. 569920) improves your safety, extend the machine’s lifetime and make maintenance more efficiently. By water, heat up and cool down faster. Also harmless to your mold and more economic than oil type for cost. Imported PID temperature controllers are used for accurate control of temperature within ±1˚C. Use imported pump for less maintenance and better durability.
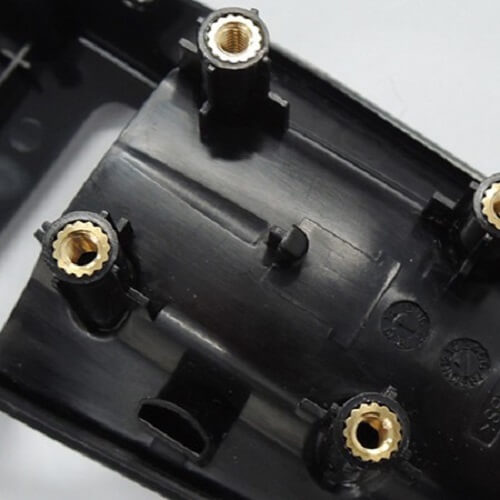
INSERT INJECTION MOLD
Categories : Injection Molds
INSERT MOLDING TECHNOLOGY: When a metal, plastic or ceramic part needs to be embedded in plastic to improve product structure it is called Insert Molding. It is a widely used process and one that YOMURA TECHNOLOGIES specializes in. With Insert Molding, a part is placed in a mold cavity then a selected plastic material is injected directly over it resulting is a single part with the insert(s) encapsulated by the material. This process normally uses engineering plastics for improved wear resistance, tensile strength and weight reduction. Insert Molding can be a highly efficient alternative to the assembly of discrete parts using soldering, connectors, fasteners, or adhesives. It also expands plastic capabilities and can reduce final product cost by limiting the amount of costly metal needed to create a part. And importantly, because we can use conventional single shot injection machines for Insert Molding, tooling costs are lower than with a multi-shot processing. Benefits: Reduced assembly and labor costs Because insert molding joins numerous components with thermoplastic, assembly and labor costs are greatly minimized. For example, a single stamping can be overmolded, then perforated to create multiple circuit paths. Reduced size and weight By eliminating fasteners and connectors, and by combining the physical strength of resin and metal inserts, insert molding yields smaller and lighter components. Increased reliability With every part tightly secured in thermoplastic, an insert molded component prevents part loosening, misalignment, improper terminations, and other problems. The thermoplastic resin also provides improved resistance to shock and vibration. Increased design flexibility Designers appreciate the virtually unlimited configurations that insert molding allows. For example, in creating a 3D circuit board, overmolding permits circuitry to move freely through the part, from inside to outside, up walls, down in holes-and the plastic ties it all together. Materials: Engineering plastic or Thermo Plastic Rubber (TPR) inserted with metal frame die casting, plated copper pin, sockets, wire frames, etc. Applications: TPR + Metal Frame(3C Mechanical Parts) ABS + Al. Die Cast (Sports/ Medical) Eng. Plastic + Patting Pin/Eng. Plastic + Wireframe (Connector) Eng. Plastic + Copper Pin/Contact (Precision Electronic Component)
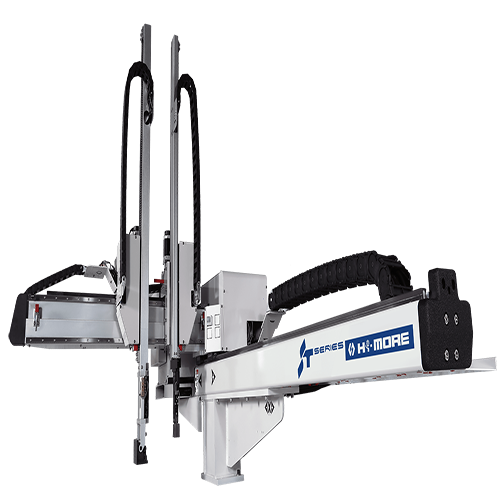
ST-800 / 900
Categories : Industrial Robots
.Improved structural design leads to greatly reduced weight. .20KG lighter than THS series .And more lightweight than HX series by around 10KG .On structure weight reduction, motors inside can work at lower load for a longer lifespan.