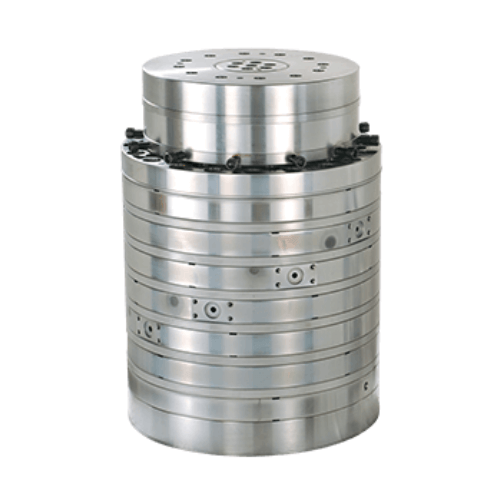
7 Layer Die Head
Categories : Extrusion Dies / Dies Heads
Die head can be manufactured to meet customer’s specific extruding capacity and bag width. Precision construction throughout assures maximum uniformity of film thickness. Die head is tempered and annealed to relieve stress, featuring deformation-free and outstanding stability. Easy to wash for convenient and fast color-change. 2~3 points temperature control. Die lip sizes are made according to customer’s requirement. HSIN LONG
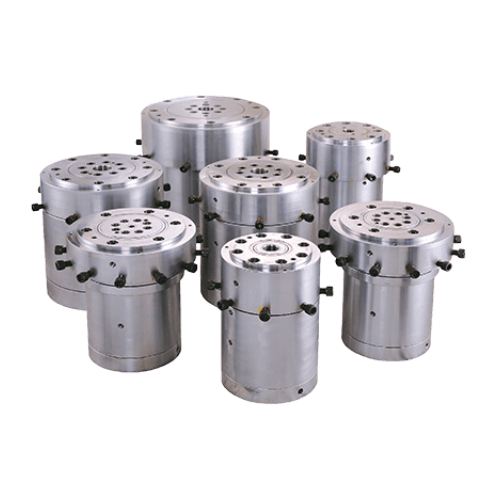
Single Layer Die Head
Categories : Extrusion Dies / Dies Heads
Die head can be manufactured to meet customer’s specific extruding capacity and bag width. Precision construction throughout assures maximum uniformity of film thickness. Die head is tempered and annealed to relieve stress, featuring deformation-free and outstanding stability. Easy to wash for convenient and fast color-change. 2~3 points temperature control. Die lip sizes are made according to customer’s requirement. HSIN LONG
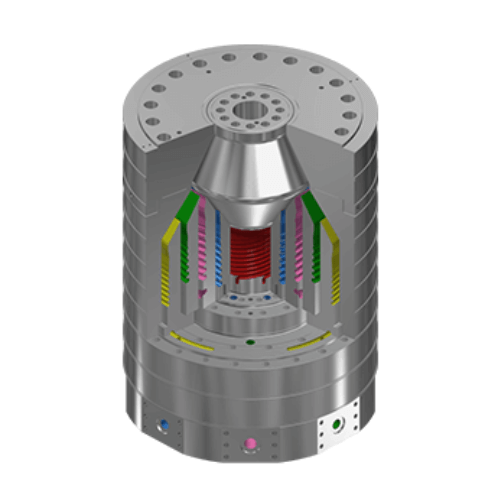
5 Layer Die Head
Categories : Extrusion Dies / Dies Heads
The Blown Film Die Head is the core component which is called the ‘‘heart’’ of the Plastic Film Blowing Machine. The main function of Die Head is to distribute the melted polymer evenly so that the thickness measured around the circumference of the tube being produced is uniform. It is the key factor to ensure a quality film. A well-designed Blown Film Die make the molten polymer travel through the Die Head smoothly without any of the polymer staying inside. A good quality melt means it does not have flow die lines on the surface which could result in defects on the film. A good Blown Film Die Head design incorporates properly constructed flow channels to allow the molten film to flow with the average speed around the circumference. Co-Extrusion Dies are another type of design allowing for speedy production of multilayered films. Co-Extrusion Dies are often used to change the structure of the layers to match the characteristic of polymers. The difference polymers affect the design of Die Head, as well. This also requires Die Head to have a short residence time. Further, the purge or change-over times are not excessive when switching from one polymer to another. HSIN LONG
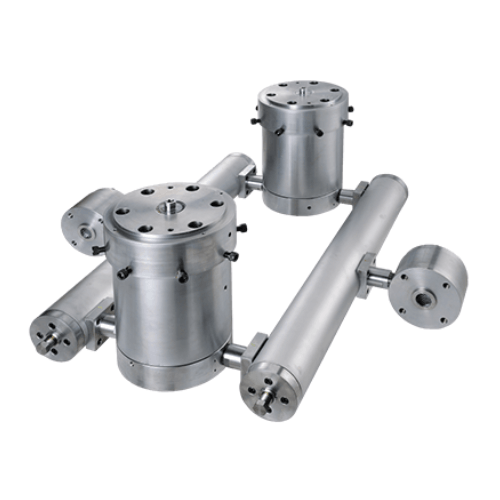
ABA Double Die Head
Categories : Extrusion Dies / Dies Heads
The Blown Film Die Head is the core component which is called the ‘‘heart’’ of the Plastic Film Blowing Machine. The main function of Die Head is to distribute the melted polymer evenly so that the thickness measured around the circumference of the tube being produced is uniform. It is the key factor to ensure a quality film. A well-designed Blown Film Die make the molten polymer travel through the Die Head smoothly without any of the polymer staying inside. A good quality melt means it does not have flow die lines on the surface which could result in defects on the film. A good Blown Film Die Head design incorporates properly constructed flow channels to allow the molten film to flow with the average speed around the circumference. Co-Extrusion Dies are another type of design allowing for speedy production of multilayered films. Co-Extrusion Dies are often used to change the structure of the layers to match the characteristic of polymers. The difference polymers affect the design of Die Head, as well. This also requires Die Head to have a short residence time. Further, the purge or change-over times are not excessive when switching from one polymer to another. HSIN LONG
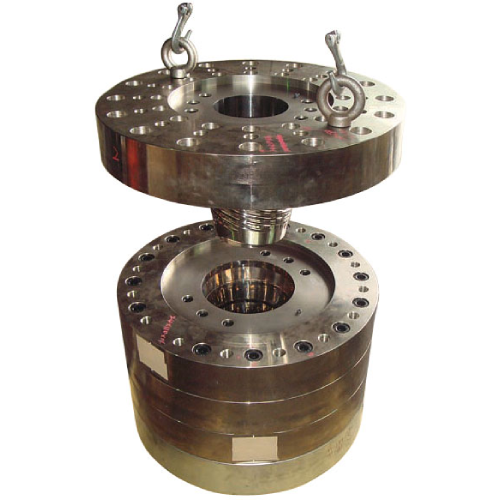
Stacked & Multilayer Type Die Heads
Categories : Extrusion Dies / Dies Heads
+For all kinds of blown film machines and it is suitable for multi-layer products. +The stacked design provides high stability & good quality.
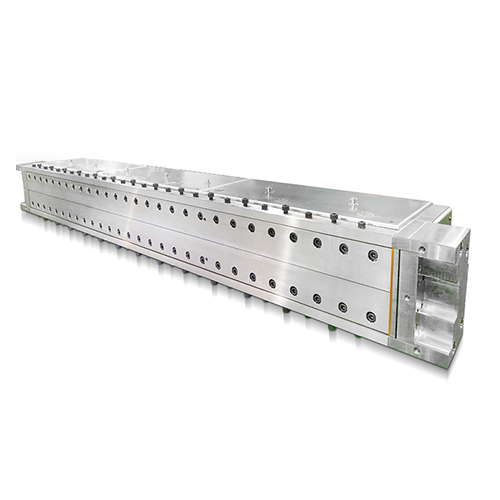
Extrusion Dies MELTBLOWN DIES
Categories : Extrusion Dies / Dies Heads
SUITABLE AVAILABLE FOR POLYMERS INCLUDING PET And PP High processing precision. Internal heating with heating rod, external heating with heating board, temperature control by heating oil cycle to ensure products of good uniformity. Meltblown filter in continuous and automated production to cut production losses more than 35%, cu costs, reliable product quality. Cut production materials consumption sharply. Featuring high yield, low power consumption, low loss, easy operation. Integrated meltblown Extrusion Die. Integrated meltblown Extrusion Die featuring precision aperture, good consistency and without maintenance wear out. Improved meltblown fiber quality and uniformity, improved product quality. Improved Extrusion Die life cycle and life span. Reduced Extrusion Die change operating time, cut maintenance cost and power consumption. Installation capacity down 30 ~ 40 KW. Cut production costs sharply.
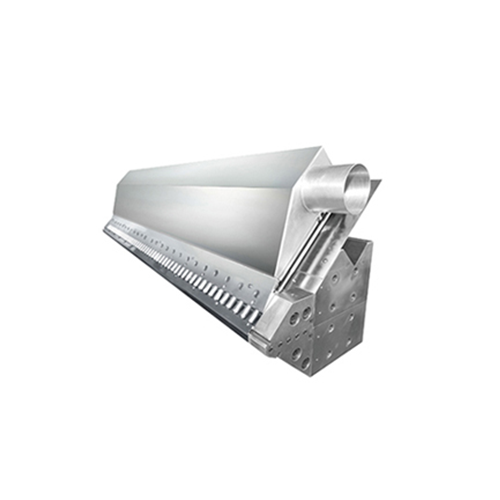
Extrusion Dies Thin Sheet
Categories : Extrusion Dies / Dies Heads
Multi-layer composite materials design, excellent polishing technique, compliant with super mirror requirements up to Ra 0.03 SUITABLE AVAILABLE FOR POLYMERS INCLUDING BOPA, BOPET, BOPI, BOPP, BOPS
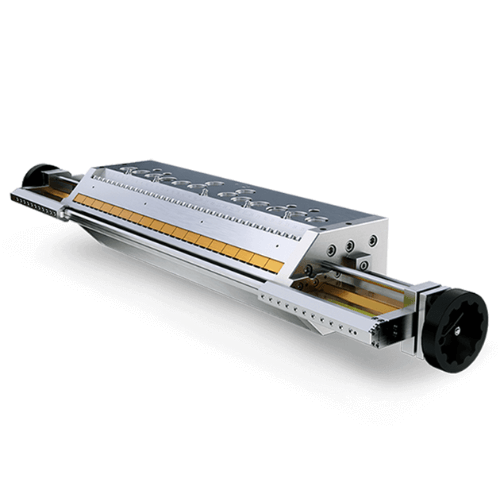
PLATE / SHEET
Categories : Extrusion Dies / Dies Heads
Composed of simple structure and segment with diversified adjustment methods. Suitable for single and multi- layers configuration in terms of customer ‘s polymer property. SUITABLE AVAILABLE POLYMER INCLUDING ABS, GPPS, MS, EVA, PA, PC, PE, PET, PP, HIPS, GPPS,PE, PET, PMMA, PVB, PVC, TPU
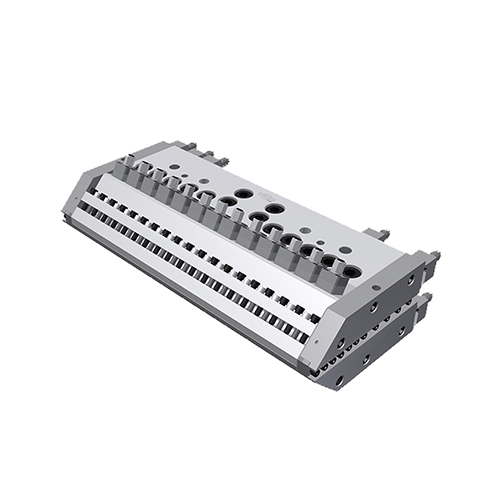
Extrusion Dies Foam Sheet
Categories : Extrusion Dies / Dies Heads
Plate sheets composite lightweight preferred. Fast tuning into foaming materials with desired thickness through flow adjustment and precision heating area. SUITABLE AVAILABLE FOAMING POLYMER INCLUDING EVA, PE, PP, PVC
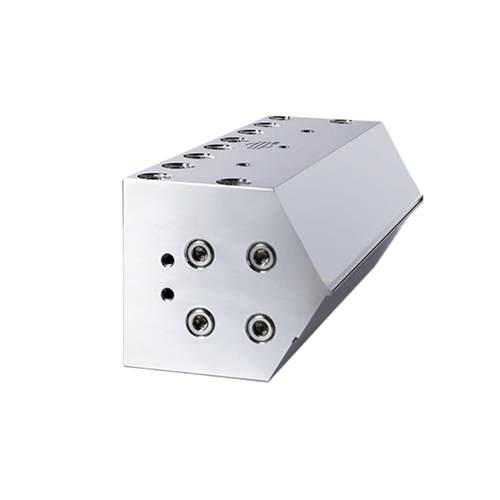
Coating Dies Slot / Slit
Categories : Extrusion Dies / Dies Heads
Slot/Slit design, excellent manifold geometry design, solvent resistant alloy, super mirror grinding technique SUITABLE APPLY TO Water Base /Oil Base / Non-Solvent Type Liquid Straightness precision is made by GMA exclusive grinding technique to reduced film thickness deviation of groove width. Interchange shim for variable lip gap application. Special stainless steel resists to a full range of solvents. Work with automated controller. Manifold geometry simulation analysis technique and optimum manifold design base on customer’s material. Uniform and stable flow distribution. No coating line defect with even thickness at high speed. Professional Slot Die maintenance service by third parties is acceptable.